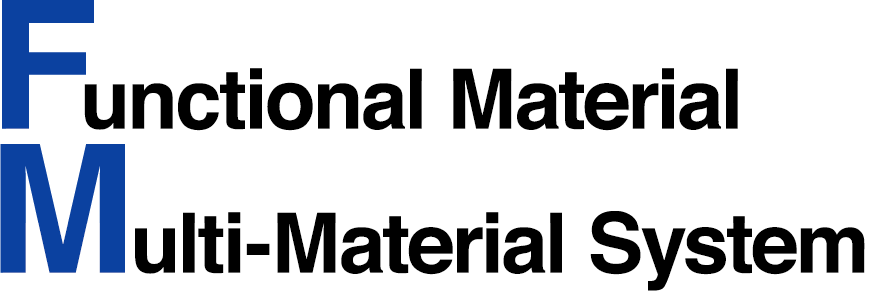
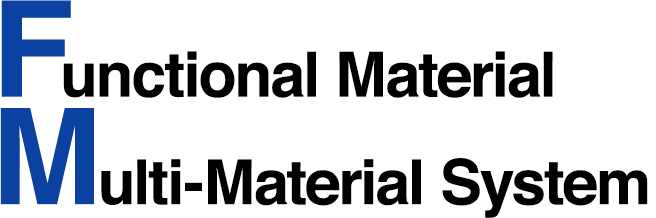
Functional Material • Multi-Material System
Structural materials for automotive white-body are gradually becoming multi—in addition to the combination of high-tensional steel with aluminum, plastic-based hybrid materials are also increasingly applied. This is true in particular for the BEVs whose weight tends to increase because of their battery and other E-components. For the BEVs equipped with advanced automated/autonomous driving systems, the use of such multi materials is being considered for lowering the weight, and for absorbing/distributing wide range of collision energy. Still, however, such metal-based materials as high-tensional steel and aluminum sustain the mainstream in the market, while the hybrid plastic types (including CFRP) are not in use as much as initially expected despite their improved processing costs and duration, bottlenecked by high material costs and their supply chain.
Meanwhile, the use of adhesives instead of such welding and mechanical joining solutions as SPOT, MIG welding and rivets is growing as new joining technology. In Europe, which is the first geographical area where this trend gained momentum, now the `Adhesive-Oriented Body Design’ concept is prevailing, driving the diversification of such materials as epoxy-/urethane-/acrylic-based and their functionalization by mixing these materials.
The following materials for components in BEV and HEVs are being used increasingly these days:
- Insulators and coefficient of thermal expansion (CTE)-mismatch-absorbers for protecting batteries and for withstanding high voltage (e.g., 800V)
- Heat-dissipating materials, while the modularization of powertrain, drivetrain and charging systems is taking place
- Friction controllers that support high-speed rotation inside transmissions
- EMI suppressors while telecommunication antennas are being diversified, integrated, and becoming more high speed
- Hybrid functionalities of electroconductive materials (e.g., hybrids of heat dissipation and EMI functionalities)
- Reutilizing of super-engineering plastics, including PPS, PA and PTFE
We have been providing the best action plans to help establish your solution development steps ahead of your market trends, and navigates automotive OEMs, tier1s and tier2s to the most appropriate direction through our continuous analyses on the latest technical and use-case trends in aforementioned onboard functional materials and structural materials across the globe, including such markets as Europe, North America and China.
Changes in technical values and market sizes of functional materials in 2020 and 2025
With regard to engineering plastics and materials, their some functionalities have not yet standardized and their mass-production methodologies have not been established. A trend of modularizing these materials and incorporating those modules with BEVs is very likely to gain momentum.
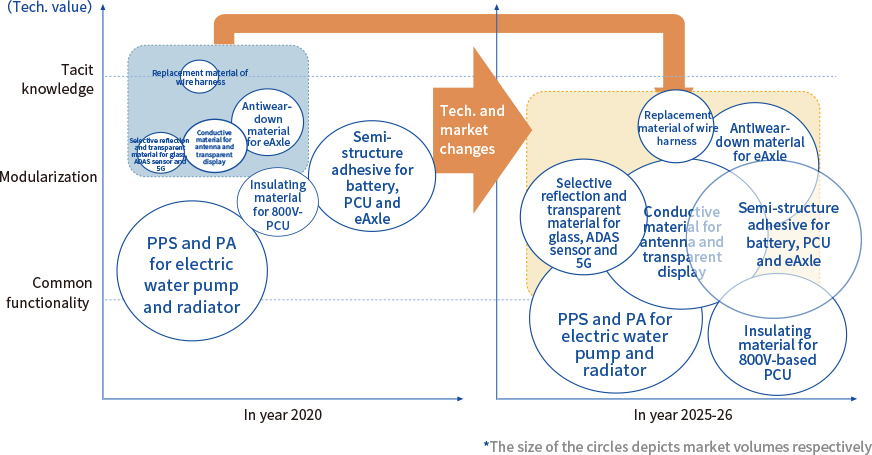